Ti-Nitride (also known as Titanium Nitride or TiN) is a game-changing material in jewelry making, particularly for PVD gold jewelry pieces. TiN has exceptional hardness, high resistance to corrosion, and vibrant golden color that makes any jewelry last long and remain elegant.
In this article, we will unveil secrets about Titanium Nitride coating for jewelry: what it is, how it looks like, the processes involved, how it protects PVD stainless steel jewelry, and many more.
What is Titanium Nitride Coating for Jewelry?
Titanium Nitride coating is a common PVD material used on jewelry (especially stainless steel jewelry) to ensure the adhesion of gold layers. It forms a golden-hued foundation that enhances the firm attachment of the bonded gold layers.
TiN is made up of Nitrogen (a non-metallic element) and Titanium (a transition metal element), which results in a tough and durable material. It is usually applied on the stainless steel base before bonding the gold layers. This creates a vibrant, long-lasting finish jewelry that’s resistant to scratches, tarnish, and corrosion, such as ion plated jewelry.
Does Titanium Nitride Look Like Gold?
Yes, Titanium Nitride has a gold appearance, just like a warm, metallic golden color. The resemblance makes it an ideal choice for creating the gold-like look in jewelry pieces without the expense of using solid gold or applying excess gold layers.
Titanium Nitride Coating Process
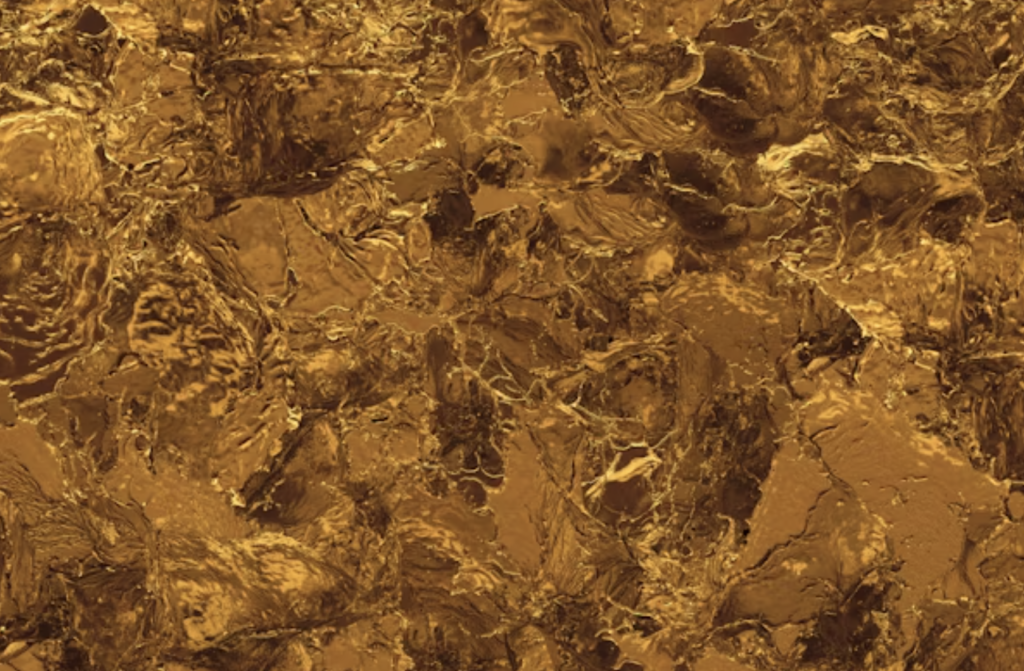
Titanium Nitride jewelry coating process is very similar to the procedure of PVD technology for stainless steel jewelry, which basically involves proper cleaning of the jewelry, to deposition of TiN, and to cooling down. The process is further explained below:
- Clean & Place in a Vacuum Chamber
It starts with manually cleaning the jewelry to remove any dirt, grease, and impurity that could affect the tight adhesion of Titanium Nitride coating. This is crucial to ensure uniform coverage of all the surfaces of the jewelry, including the edges.
After the manual cleaning is done, carefully position the jewelry in a vacuum chamber to eliminate any remaining contaminants and prepare for coating.
- Deposition
While the jewelry is in the vacuum chamber and exposed to a high temperature plasma, titanium nitride is poured inside. The high temperature plasma breaks down the titanium nitride molecules into ions, which are then deposited onto the surface of the jewelry with high force. This results in tight adhesion of the TiN on the jewelry surface.
- Cooling Down
After the deposition process is completed, the jewelry is left to cool down and stabilize the titanium nitride layer. This step is important in making sure the coating adheres securely, hardens properly, and achieves its final gold-like finish.
Once this is done, the jewelry is then ready for additional plating like gold plating.
How Can the Ti-Nitride Layer Protect PVD Stainless Steel Jewelry
Compared to traditional electroplating, PVD ensures better color retention and longevity because of the inclusion of TiN. Titanium coating on stainless steel stands out as one of the processes to preserve your jewelry durability and color.
- Hardness
TiN layer is one of the hardest thin-film coatings, with a rating of 8-9 on the Mohs scale. Its toughness provides a robust barrier that protects the jewelry from friction, prevents scratches, abrasions, and general wear or tear.
- Water Resistance
Ti-Nitride coating is highly resistant to water and does not react with stainless steel jewelry. It doesn’t also react to tissue, blood, skin, bones, or body fluids, making it hypoallergenic and safe from rust, corrosion, or tarnish even when exposed to humid environments.
Hence why titanium nitride jewelry pieces easily retain their vibrant color and structural integrity.
Ti-Nitride Applications in Other Industries
Ti-Nitride coating is often used in many other industries to enhance their products appearance and prolong their lifespan. They include:
- Medical Industry: Ti-Nitride coating is applied on surgical instruments, dental tools, and implants because of its biocompatibility, hardness, and resistance to corrosion. The coating improves durability, reduces friction, and minimizes the risk of contamination, resulting in safety medical procedures.
- Aerospace Industry: TiN coating is used on engine components, turbine blades, and fasteners to prevent friction, extreme temperatures, and oxidation. The coating ensures the components can endure flight harsh conditions while maintaining top-quality performance.
- Cutting Tools: Drills, saw blades, and milling equipment are often coated with Titanium Nitride to curb friction, extend the tool life, and enhance cutting efficiency. The coating is very important when the cutting tools are used for tough materials.
- Automotive: Titanium Nitride coating is applied to engine parts, gear systems, and suspension components for its ability to reduce friction and wear. The coating ensures better performance, fuel efficiency, and reliability under high stress or adverse temperature conditions.
Conclusion
Titanium Nitride coating contributes largely to the durability, appearance, and longevity of PVD gold-plated jewelry. Its exceptional hardness and water resistance protects the underlying jewelry (usually stainless steel) from scratches and tarnishing, and also ensures applied gold layers stay firmly on the jewelry. TiN has a gold-like look, making the jewelry piece share high resemblance with real gold.
This advanced coating approach is a perfect blend of beauty, durability, and affordability, which is why it’s important to only contact a professional stainless steel jewelry manufacturer with years of experience to get the best Ti-Nitride-protected pieces.