Over the years, traditional methods like casting and forging have been the most popular for crafting metals into jewelry manufacturing. These methods have continually shown to be unsuitable for complex, intricate designs, and produces a lot of waste.
But with the introduction of Powder Metallurgy (P/M), crafting of metals in jewelry manufacturing has become easier, more efficient, and environmentally-friendly.
In this post, we will explain in-depth what powder metallurgy is and its benefits in jewelry manufacturing.
What is Powder Metallurgy?
Powder metallurgy (PM) is a process that involves blending fine metal powders, compacting them into desired shapes, and then sintering them—heating just below the melting point—to form solid, bonded metal parts. This technique produces strong, homogenous metal pieces, allowing for accurate control over the metal features.
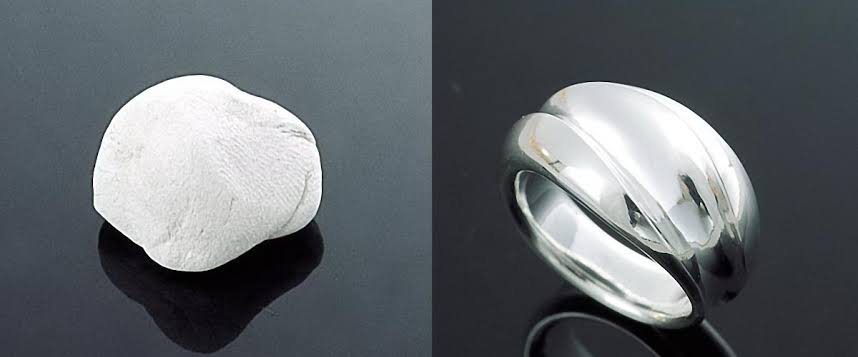
Source: Jewelry Education
PM is often used in the jewelry industry to create intricate designs and shapes that would be difficult or impossible to produce using traditional methods.
Common Metals Used for Powder Metallurgy
The common metals used for powder metallurgy in jewelry manufacturing are precious metals like gold, silver, palladium, copper, along with their alloys. They are preferred for their high melting points, corrosion resistance, and aesthetic appeal, making them ideal for creating durable and attractive jewelry.
Powder Metallurgy Process in Jewelry Manufacturing
How does powder metallurgy work in jewelry making? Powdered metal manufacturing consists of 3 basic steps, which are:
Step 1: Powder Blending
The powder metallurgy process starts with selecting and blending the right metals like gold, silver, or alloys, to achieve the desired composition, color, and properties. Blending different metal metallurgy materials produces unique colors and textures, which are very important in creating top-quality jewelry pieces.
Step 2: Die Compaction
The blended powder is pressed into a die or mold under high pressure. This results in a “green” part, which has the shape and size of the desired jewelry.
NOTE: The powder metallurgy compaction determines the jewelry’s final form, as it produces the shape and density of the piece. So, it must be done in a well-fabricated mold and under high pressure.
Step 3: Sintering
During powder metallurgy sintering, the green parts are inserted into a furnace, where they are heated below their melting points. The heat causes the metal particles to bond and solidify, thereby creating a durable and wear-resistant jewelry.
Sintering stainless steel offers the ability to produce finely detailed jewelry with excellent structural integrity. Secondary operations like applications of CNC machining in jewelry making can be used to enhance powder metallurgy forging.
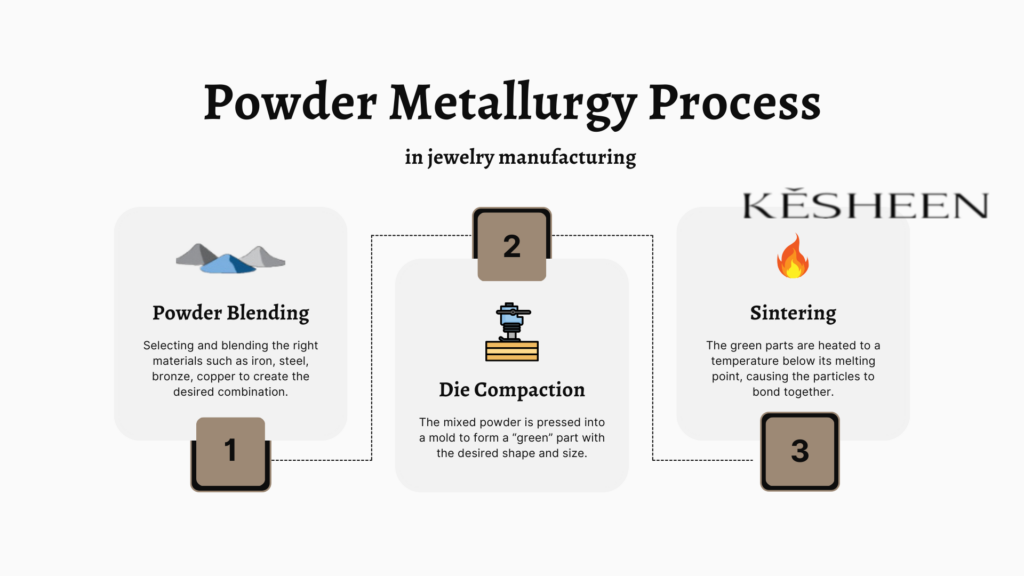
Advantages of Powder Metallurgy in Jewelry Making
These are some of the benefits of powder metallurgy in jewelry making:
- Capable of Complex and Intricate Designs
Powder metallurgy can be used to create complex and intricate designs, even for extremely hard stainless steel jewelry. Since the metal powder is compacted into a precise die, jewelry pieces can be easily produced in delicate patterns, fine textures, and intricate shapes.
- High Precision, Consistency, and Intricacy
PM helps with excellent control of the final product’s shape and features. It guarantees that each piece meets its exact specifications, with exceptional detail, enhancing the jewelry’s quality and aesthetic appeal.
- Versatility in Material Choices
This manufacturing technique supports a wide range of alloys, including gold, silver, platinum, palladium, and copper. Precious metal alloys are often used to create high-end jewelry, while copper alloys are more commonly used in fashion jewelry.
- Exceptional Wear and Strength
Jewelry pieces made using powder metallurgy are durable and resistant to wear. PM strengthens the bonds between metal particles, improving jewelry strength and hardness to withstand daily use.
- Material Saving and Environmental-friendly
Since the powder metallurgy materials are compacted into the exact shape needed, there’s little waste. Moreover, any leftover powder can be reused, making the process a more sustainable jewelry manufacturing technique for keeping the environment safe.
- Lower Production Cost for Large Volumes
Once established, powder metallurgy processes are cost-effective for large-scale production due to the high repeatability and reduced machining needs. Also, PM requires only little secondary processing, making it a great tool for meeting bulk orders.
Powder Metallurgy vs. Casting in Jewelry Manufacturing
Casting and powder metallurgy are two popularly used methods in jewelry manufacturing, yet they differ in processes and benefits. Below is a comparison of powder metallurgy vs. casting:
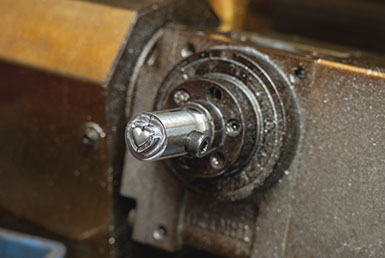
1. Production Process
- Powder Metallurgy: Involves blending metal powders, compacting them in a die to form the desired shape, and sintering to bond particles at high temperatures. This process simplifies stainless steel jewelry manufacturing methods.
- Casting: Involves pouring molten metal into a mold, where it cools and hardens. The finished parts don’t always come out accurately, thus requiring additional processing.
2. Precision and Complexity
- Powder Metallurgy: Ideal for high-precision, complex shapes with minimal need for further processing. It supports intricate, uniform designs with excellent dimensional accuracy and lower defects.
- Casting: While casting can produce precise pieces, it can be more susceptible to variations due to factors like mold shrinkage, air bubbles, and metal flow and ften requires post-processing to achieve precision.
3. Cost and Efficiency
- Powder Metallurgy: Involves fewer and more simple production steps, saving both time and cost. This makes it a better option to manage materials and fulfill orders before the due date.
- Casting: Generally cost-effective both small and large production runs.
4. Application Fields
- Powder Metallurgy: Often used to create high-precision and complex jewelry pieces that require great strength, fine detailing, & uniformity like rings and pendants.
- Casting: Widely used for high-volume production of gold, silver, and other precious metal jewelry like statement necklaces and rings.
5. Environmental Impact
- Powder Metallurgy: Produces lesser waste. Its high material utilization rate can reach 95%, making it far superior to casting processes. And leftovers can be easily recycled for another production.
- Casting: Requires more energy, has longer production cycles, and causes a negative environmental footprint because of its melting process.
Key Takeaway
Powder metallurgy stands out among other manufacturing methods when making intricate and complex jewelry pieces. It offers numerous benefits, such as create high-precision jewelry, support versatile material choices, curb waste, save cost, maintain a sustainable environment, and so on.
To get exquisite stainless steel metallurgy jewelry pieces that will elevate your brand, make sure to reach out to a professional stainless steel jewelry manufacturer.